Manufacturing environments are full of moving parts, quite literally. And when something goes wrong, how quickly and clearly you capture that incident can be the difference between a near-miss and a costly compliance headache.
If you’re a health and safety lead, site manager, or operations director looking into incident reporting software, you’re in the right place. Let’s cut through the noise and talk about what actually matters, what to look for, what to avoid, and how to pick a tool that doesn’t become yet another admin burden.
Helpful summary
Overview: This guide walks through the must-have features (and the red flags) of incident reporting software for UK manufacturing teams. It also includes insights into how Evalu-8 EHS stacks up as an all-in-one solution.
Why trust us: Evalu-8 supports health and safety teams in high-risk sectors like manufacturing, construction, and rail, where rapid, accurate incident reporting is essential.
Why it matters: Choosing the right software doesn’t just keep your business compliant, it helps reduce downtime, improve worker safety, and support a strong safety culture.
Action points: Prioritise platforms with real-time reporting, mobile access, built-in workflows, and automatic audit trails. Skip anything that’s clunky, outdated, or lacks UK-specific compliance tools.
Further research: Learn how Evalu-8 EHS helps manufacturing businesses get ahead of risk, not just respond to it. Book a no-pressure walkthrough on our website.
Why incident reporting software matters on the factory floor
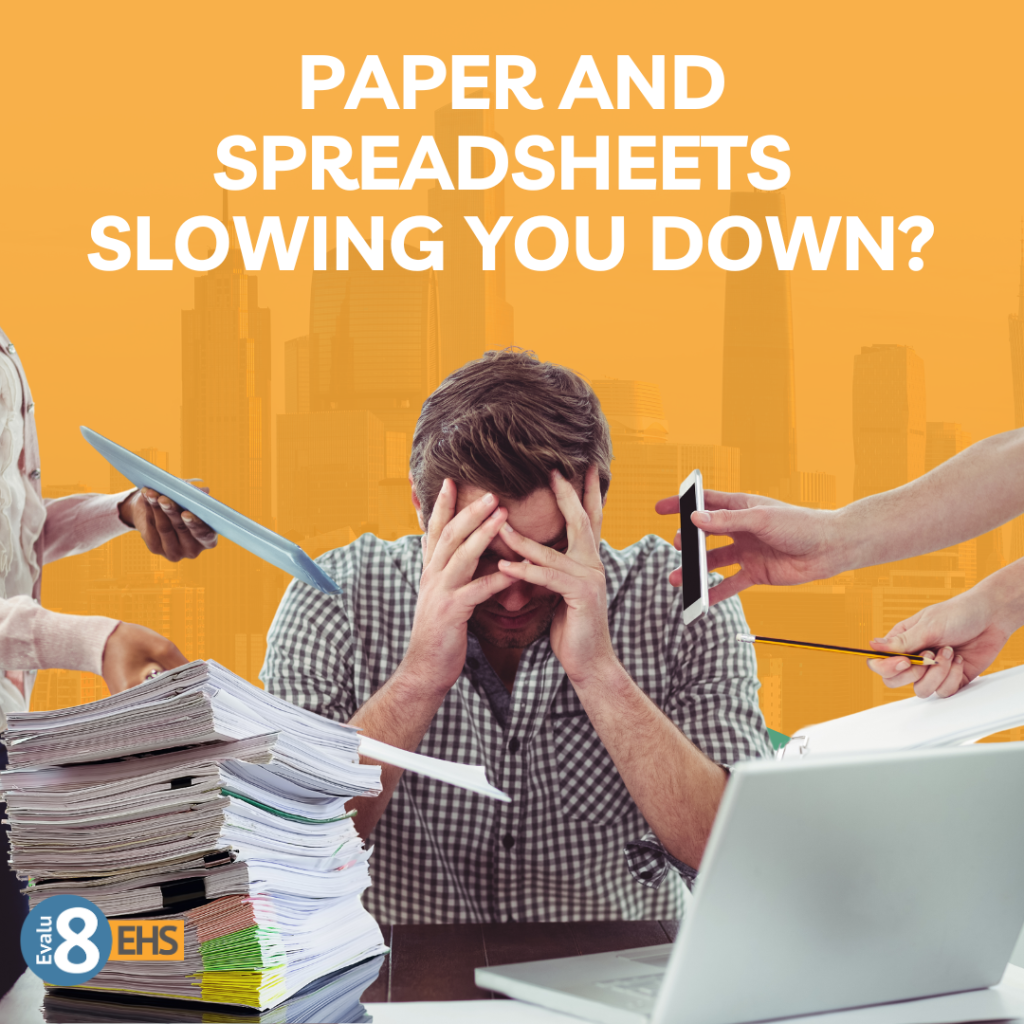
Let’s be honest, paper-based reporting systems or clunky spreadsheets just don’t cut it anymore. They’re slow, hard to track, and easy to lose in the chaos of a busy manufacturing site.
Incident reporting software helps you:
Capture accidents, near misses, and hazards in real time
Track follow-up actions and investigations automatically
Generate accurate, exportable reports for audits and board meetings
Stay compliant with HSE guidance and ISO standards
In short, it takes the admin off your hands and gives you visibility instead.
What to look for in incident reporting software (especially if you’re in manufacturing)
1. Real-time reporting with mobile access
You can’t wait until the end of a shift to report an incident. The best platforms let users report from any device, phone, tablet, or desktop, while on site, with photos, location tagging, and voice-to-text options. That immediacy protects your people and your paper trail.
2. Built-in workflows for follow-up and investigations
Logging an incident is just step one. What happens next matters more. You need a tool that kicks off investigations, assigns tasks, sets deadlines, and lets you track corrective actions, all within the same system. No toggling between emails, spreadsheets, and shared drives.
3. Integration with your wider health and safety system
Manufacturing businesses deal with risk assessments, PPE, training records, COSHH, fatigue, and more. Your incident reporting software should link with the rest of your health and safety processes, so nothing gets missed and your reports are always up to date.
Watch out for these red flags
Not all software is created equal. If you’re shopping around, here are a few things to be wary of:
Hidden costs for essential features
Be cautious of platforms that charge extra for basics like mobile access, user permissions, or exporting reports. It’s not just frustrating, it’s bad budgeting.
Poor UX or slow performance
If it takes more than a few minutes to log a single incident, your team won’t use it. You want something intuitive, with clear navigation and minimal training required.
Lack of UK compliance focus
Some tools are designed with American OSHA standards in mind, which don’t always match up with UK HSE expectations. Make sure the platform supports RIDDOR reporting and aligns with UK legislation.
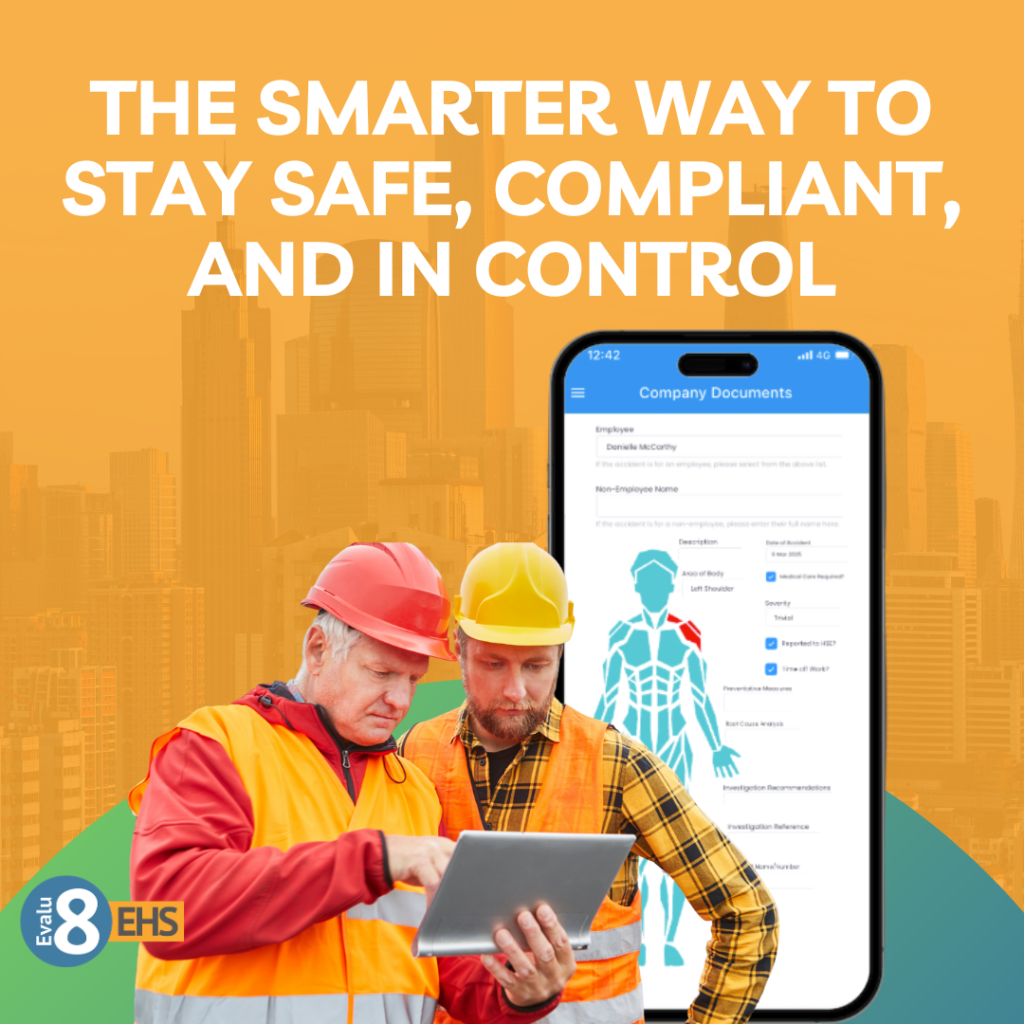
Why Evalu-8 EHS is the smart choice for manufacturers
Easy incident capture from any device
Team members can log incidents instantly using their phone or tablet, even while on the shop floor. Add photos, voice notes, GPS data, whatever gives you the full pictures.
Explore how to log an accident on Evalu-8
Automatic workflows and escalations
Once an incident is logged, the software automatically notifies the right people, kicks off an investigation, and tracks every action taken. Nothing gets missed or delayed.
Linked modules for full visibility
Evalu-8 isn’t just incident software, it’s a complete EHS platform. Incidents feed into risk assessments, fatigue monitoring, training records, audits, and more. So you see cause and effect, not just isolated events.
UK compliance as standard
With built-in tools for RIDDOR, document storage, audit trails, and inspection tracking, you’ll always have what you need for regulatory peace of mind.
And best of all? It’s genuinely easy to use. No 100-page user manual or weeks of onboarding.
Common mistakes to avoid when choosing incident reporting software
Let’s quickly recap the traps many manufacturers fall into:
Choosing the cheapest option, only to discover hidden costs later
Buying a system designed for office work, not high-risk industries
Failing to involve end users in the decision-making process
Ignoring mobile access and real-time capability
Settling for a tool that doesn’t integrate with the rest of your safety systems
Think of it this way: if your team doesn’t use the system properly, the data is worthless. That’s why ease of use, automation, and integration should be top of your checklist.
Final thoughts: Get proactive with your safety reporting
The best manufacturers don’t just respond to incidents, they learn from them. With the right software, you don’t just capture what went wrong. You understand why it happened, what to do about it, and how to prevent it next time.
Evalu-8 EHS gives you that edge. A full, real-time, mobile-friendly platform that doesn’t just tick boxes, but transforms your safety culture. If you’re ready to raise the bar, we’re here to help.
Curious about incident reporting software? Your questions answered
Speed and accuracy. Good software captures incidents in real time, not hours later, and gives you a full digital audit trail to support investigations and compliance.
With Evalu-8 EHS, yes. Reports can be logged even without signal, and will sync automatically once the device is back online. Ideal for remote or high-interference areas.
Absolutely. You can log near misses, hazards, accidents, and environmental incidents all from the same platform—and track corrective actions with full visibility.
Yes. Whether you operate across one location or twenty, you’ll get a central dashboard and the ability to assign user permissions by site, department, or role.
Most teams are fully up and running within a couple of weeks. Our support team will guide you through setup, import any existing data, and train your team so they’re confident from day one.