Chemicals are an integral part of many workplaces, but their improper handling and storage can pose serious risks to both employees and the environment. To ensure the safety of everyone in your workplace, it is essential to follow proper Environmental, Health, and Safety (EHS) measures. In this guide, we will explore the importance of chemical safety in the workplace and provide practical tips on how to implement EHS guidelines effectively.
Understanding the Importance of Chemical Safety in the Workplace
Safety should always be a top priority in any workplace, especially when it comes to chemicals. EHS plays a crucial role in ensuring a safe working environment by proactively identifying and mitigating potential risks. By adhering to EHS guidelines, you not only protect your employees’ health but also safeguard your business from costly accidents, lawsuits, and damage to the environment.
The Role of EHS in Ensuring Safety
Environmental, Health, and Safety (EHS) teams are responsible for developing and implementing safety protocols in the workplace. These teams consist of dedicated professionals who have a deep understanding of the potential risks associated with chemicals and the necessary measures to mitigate them.
One of the key responsibilities of EHS teams is to conduct thorough risk assessments. They carefully analyze the chemicals used in the workplace, identifying their hazardous properties and potential risks. This comprehensive evaluation allows them to develop effective safety measures that minimize the likelihood of accidents and injuries.
Once the risks are identified, EHS teams establish safety procedures and guidelines that must be followed by all employees. These protocols include proper handling, storage, and disposal of chemicals, as well as the use of personal protective equipment (PPE) such as gloves, goggles, and respirators. By providing clear instructions and guidelines, EHS teams ensure that employees are equipped with the knowledge and tools necessary to work safely with chemicals.
Furthermore, EHS teams play a crucial role in providing training to employees. They conduct regular workshops and sessions to educate workers about the potential hazards associated with different chemicals and how to handle them safely. These training programs not only raise awareness but also empower employees to take responsibility for their own safety and the safety of their colleagues.
Monitoring compliance is another important aspect of EHS teams’ responsibilities. They regularly inspect the workplace to ensure that safety protocols are being followed and identify any areas that require improvement. By actively monitoring and enforcing compliance, EHS teams create a culture of safety and accountability within the organization.
The Impact of Chemical Hazards on Employee Health
Chemical hazards can have severe consequences on employee health if not handled properly. Exposure to toxic substances can lead to respiratory issues, skin irritations, burns, and even long-term health problems. It is essential for employers to recognize the potential risks and take necessary precautions to protect their employees.
By prioritizing chemical safety, you demonstrate your commitment to protecting your employees’ well-being and fostering a healthy work environment. Implementing safety measures and providing proper training not only reduces the risk of accidents but also improves overall employee morale and productivity.
Moreover, by ensuring chemical safety, you contribute to the well-being of the community and the environment. Accidental releases or improper disposal of hazardous chemicals can have far-reaching consequences, such as contaminating air, water, and soil. By adhering to EHS guidelines, you minimize the environmental impact of your operations and contribute to sustainable practices.
It is important to note that chemical safety is an ongoing process. As new chemicals and technologies emerge, EHS teams must stay updated and adapt their safety protocols accordingly. Regular reviews and assessments should be conducted to identify any changes or improvements that need to be made in order to maintain a safe working environment.
In conclusion, chemical safety is of utmost importance in the workplace. By prioritizing the well-being of your employees and the environment, you not only mitigate potential risks but also create a culture of safety and responsibility. Through the efforts of EHS teams and the implementation of effective safety protocols, you can ensure a safe and healthy working environment for everyone.
Identifying Common Chemical Hazards in the Workplace
Before implementing safety measures, it is crucial to be aware of the potential chemical hazards present in your workplace. Understanding the different types of chemical hazards and recognizing hazardous symbols is key to preventing accidents and minimizing risks.
Chemical hazards can be classified into various categories, including flammable, corrosive, toxic, and reactive substances. Each type poses its own unique risks and requires specific safety measures. By familiarising yourself with these hazards, you can take appropriate precautions to prevent accidents.
Flammable substances are those that can easily catch fire when exposed to heat, sparks, or open flames. They can ignite and cause fires or explosions, putting both life and property at risk. Examples of flammable substances commonly found in the workplace include gasoline, solvents, and certain gases.
Corrosive substances are highly reactive and can cause severe damage to living tissue upon contact. They can burn the skin, eyes, and respiratory system, leading to serious injuries or even death. Some common corrosive substances include strong acids, alkalis, and certain cleaning agents.
Toxic substances are those that can cause harm to human health when inhaled, ingested, or absorbed through the skin. They can lead to acute or chronic health effects, ranging from mild irritation to organ damage or even cancer. Examples of toxic substances include certain pesticides, heavy metals, and some solvents.
Reactive substances are highly unstable and can undergo rapid chemical reactions when exposed to heat, light, or other chemicals. These reactions can release toxic gases, generate heat or explosions, and cause significant damage to the surroundings. Examples of reactive substances include certain oxidizers, peroxides, and unstable compounds.
Chemicals often come with warning labels or symbols indicating their hazards. These symbols provide vital information to employees about possible risks associated with the substance. The most commonly used symbols include the flame symbol for flammable substances, the skull and crossbones symbol for toxic substances, the exclamation mark symbol for irritants, and the corrosion symbol for corrosive substances.
It is essential to ensure that all employees are trained to recognize and understand these symbols to avoid any mishaps. This training should include information on the specific hazards associated with each symbol and the appropriate safety measures to be taken when working with or around these substances.
By identifying the common chemical hazards in your workplace and educating your employees about them, you can create a safer work environment and reduce the risk of accidents and injuries. Regular safety audits and inspections should also be conducted to ensure that all necessary precautions are in place and that employees are adhering to the established safety protocols.
Implementing EHS Guidelines for Chemical Safety
To effectively implement EHS guidelines in your workplace, you need to focus on two critical aspects: proper storage of chemicals and safe handling and usage.
Proper Storage of Chemicals
Storing chemicals in a safe and organised manner is essential to minimize the risk of accidents. Segregate incompatible substances, use appropriate containers, and ensure proper labeling to avoid confusion. Regularly inspect storage areas and dispose of expired or unnecessary chemicals. By establishing clear storage protocols, you can mitigate potential hazards and promote a safe working environment.
Safe Handling and Usage of Chemicals
When working with chemicals, it is crucial to follow safety procedures at all times. Provide employees with proper personal protective equipment (PPE) and train them on how to use it correctly. Encourage the use of engineering controls, such as ventilation systems, to minimize exposure. Additionally, ensure that employees are aware of emergency protocols, such as eyewash stations and showers, in case of accidental exposure.
Emergency Response to Chemical Incidents
Despite our best efforts, accidents can still happen. Being prepared for chemical incidents is essential to minimize their impact and provide immediate assistance to affected individuals.
First Aid Measures for Chemical Exposure
Train employees on basic first aid procedures for chemical exposure. This includes rinsing affected areas with water, removing contaminated clothing, and seeking medical attention when necessary. Quick and appropriate first aid measures can often prevent further harm and ensure a faster recovery.
Reporting and Investigating Chemical Incidents
Establish a reporting system for chemical incidents and encourage employees to report any accidents, spills, or near misses promptly. Investigate the root causes of incidents to identify areas for improvement and implement corrective actions to prevent similar occurrences in the future. By learning from past experiences, you can continually enhance safety practices in your workplace.
Training and Education for Chemical Safety
Training and education are fundamental for creating a culture of safety in the workplace. Regularly providing relevant safety training ensures that employees stay informed and capable of handling chemicals safely.
Importance of Regular Safety Training
Keep your employees up to date with the latest safety regulations and best practices through regular training sessions. Encourage their active participation and address any questions or concerns they may have. By empowering your employees with knowledge, you create a safer working environment and instill a sense of ownership in chemical safety.
Creating a Culture of Safety in the Workplace
Safety should be a shared responsibility among all employees. Foster a culture of safety by promoting open communication, recognizing and rewarding safe practices, and encouraging everyone to actively participate in safety initiatives. When employees feel empowered and invested in safety, they become the first line of defense against potential hazards.
By prioritising chemical safety in your workplace, you not only protect your employees and the environment but also strengthen your business by mitigating risks and fostering a positive work atmosphere. Remember, it’s everyone’s responsibility to ensure a safe working environment. Let’s work together to create a workplace free from chemical hazards!
More from the EHS Blog
Watch a 5 minute video of Evalu-8 EHS
“It has brought all of our health and safety under one roof and made it easy for me to see all the data”
Get to see exactly how our software can work within your current processes to help your organisation grow a positive safety culture.
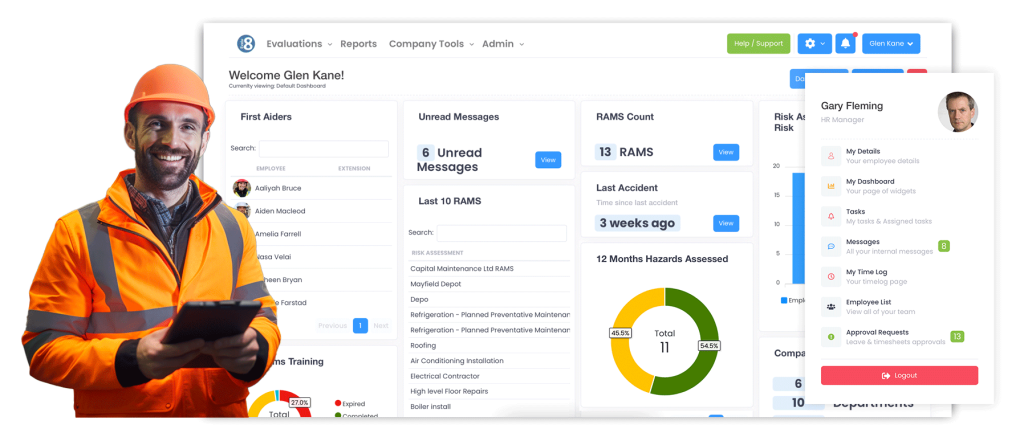
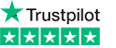
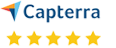