Managing incidents effectively in manufacturing isn’t just about reacting quickly, it’s also about how well you report them. Unfortunately, many UK manufacturers unknowingly make reporting mistakes that lead to more incidents. These mistakes can put employees at risk and cause costly downtime. Let’s explore five common pitfalls and discuss practical steps to avoid them, helping your team create a safer workplace.
Helpful Summary
Overview: This article outlines five frequent reporting errors in manufacturing workplaces, highlighting their impact and providing actionable advice to prevent them.
Why Trust Us: Evalu-8 EHS is trusted by manufacturing businesses across the UK to simplify incident reporting, improve safety compliance, and reduce workplace risks.
Why It Matters: Accurate reporting directly contributes to employee safety, reduces risk, and helps maintain regulatory compliance, all essential for successful manufacturing operations.
Action Points: Use Evalu-8 EHS software to streamline your incident reporting processes, reduce common errors, and improve your safety management practices immediately.
Further Research: Visit the Evalu-8 EHS Knowledge Centre to explore additional resources on effective incident reporting and risk management.
Mistake 1: Delayed reporting of incidents
One of the biggest mistakes manufacturing companies make is delaying incident reporting. Waiting to report incidents can lead to important details being forgotten or misunderstood, creating a higher risk of similar incidents happening again.
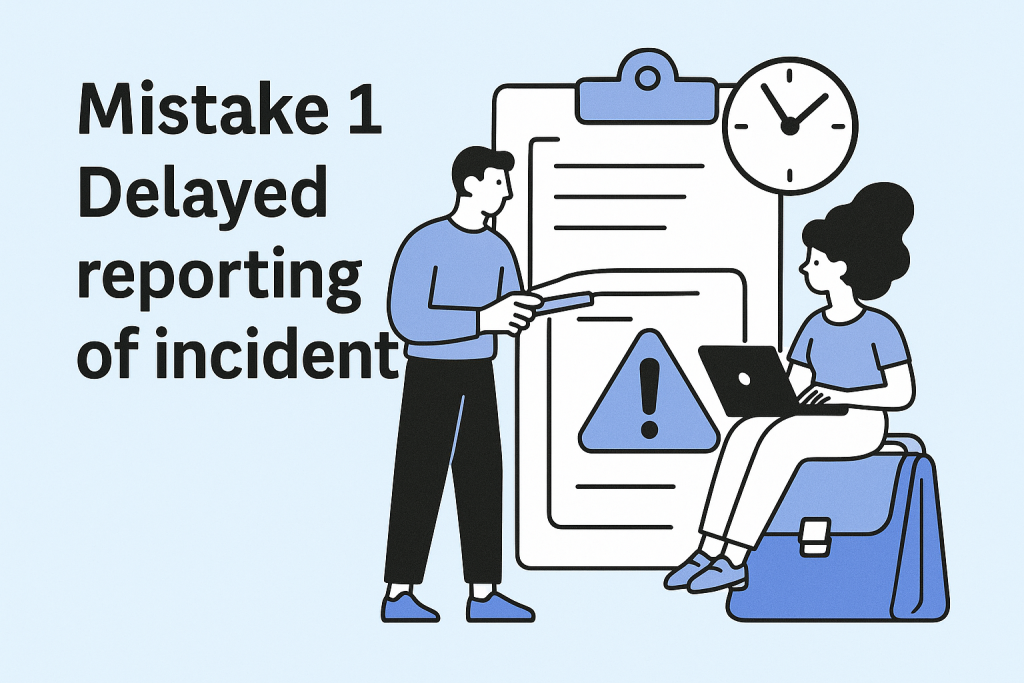
How to fix it:
Encourage immediate reporting with simple digital tools like Evalu-8 EHS. Its mobile app allows employees to report incidents instantly from anywhere on the factory floor. By capturing details straight away, you ensure that information is accurate and timely, significantly reducing future risks.
Mistake 2: Incomplete or unclear reports
Poor-quality reports lacking key details are common and dangerous. If you don’t understand exactly what happened, you can’t stop it from recurring. Reports should clearly state what occurred, when, why, and who was involved.
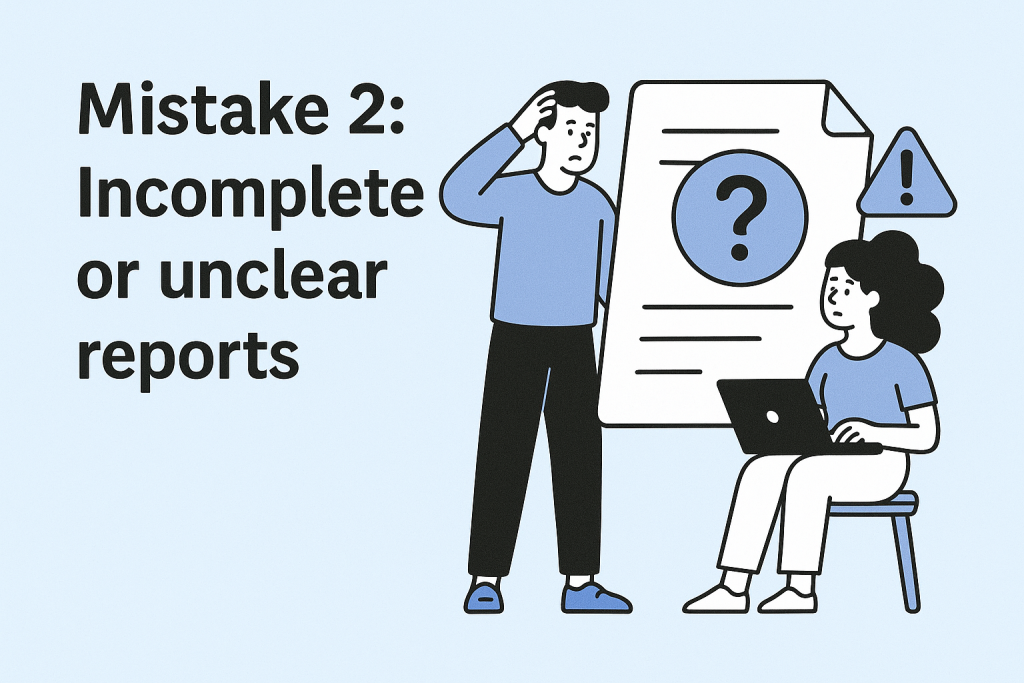
How to fix it:
Implement structured reporting forms. With Evalu-8 EHS, you have access to easy-to-follow digital templates guiding your team to provide complete, concise information. Prompts within the software ensure no vital details are missed, keeping your incident documentation crystal clear.
Mistake 3: Not tracking near misses properly
It’s tempting to overlook near misses because “nothing bad actually happened”. However, near misses are valuable warnings of potential serious incidents. Ignoring them is a common but risky mistake.
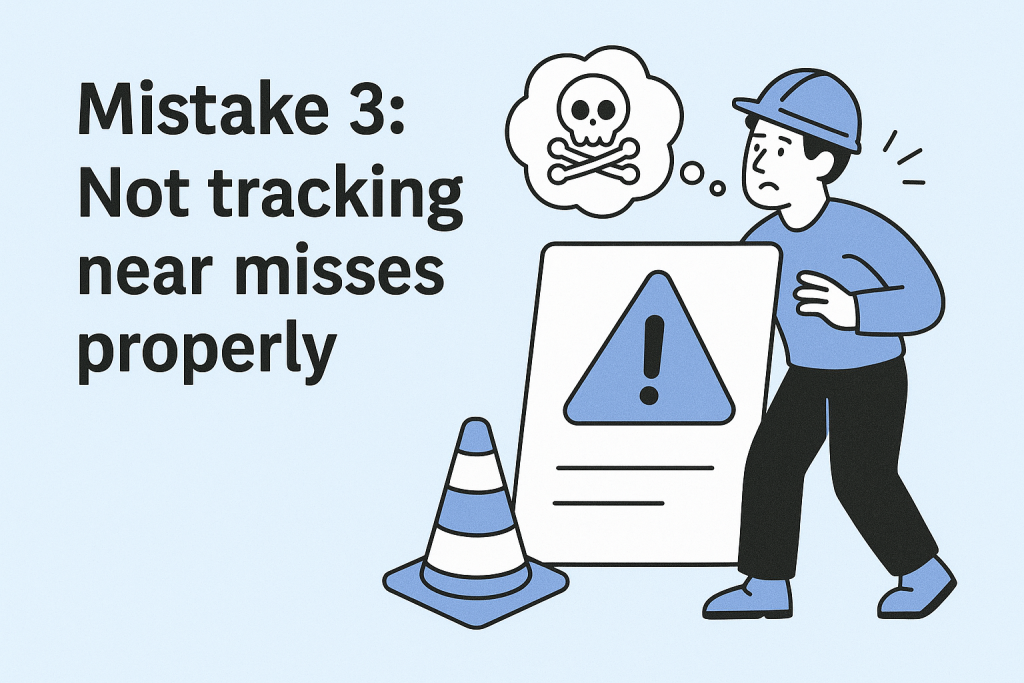
How to fix it:
Make near-miss reporting straightforward and reward proactive safety reporting. Evalu-8 EHS helps track near misses with dedicated logging features, enabling you to identify patterns and prevent future incidents before they occur. Encouraging staff to report all safety concerns enhances overall vigilance.
Mistake 4: Failing to analyse incident data
Many manufacturers log incidents but never fully analyse them. Without analysis, incidents keep repeating. If you don’t understand trends or underlying causes, you’ll always be fighting fires rather than preventing them.
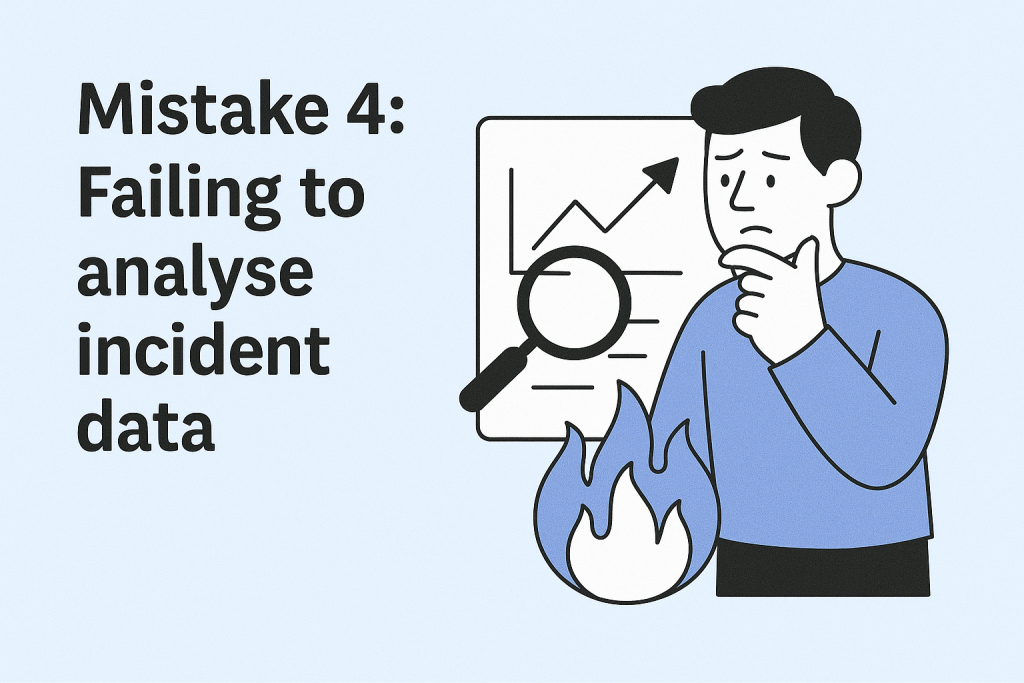
How to fix it:
Use Evalu-8 EHS analytics tools to automatically generate insightful reports. Its powerful dashboards visualise data clearly, identifying recurring incidents or trends. With better data, your team can confidently take preventive measures to stop incidents from recurring.
Mistake 5: Poor communication after incidents
Finally, poor communication following incidents leads to confusion and repeated errors. Staff need to clearly understand what happened, why, and what they should do differently in the future.
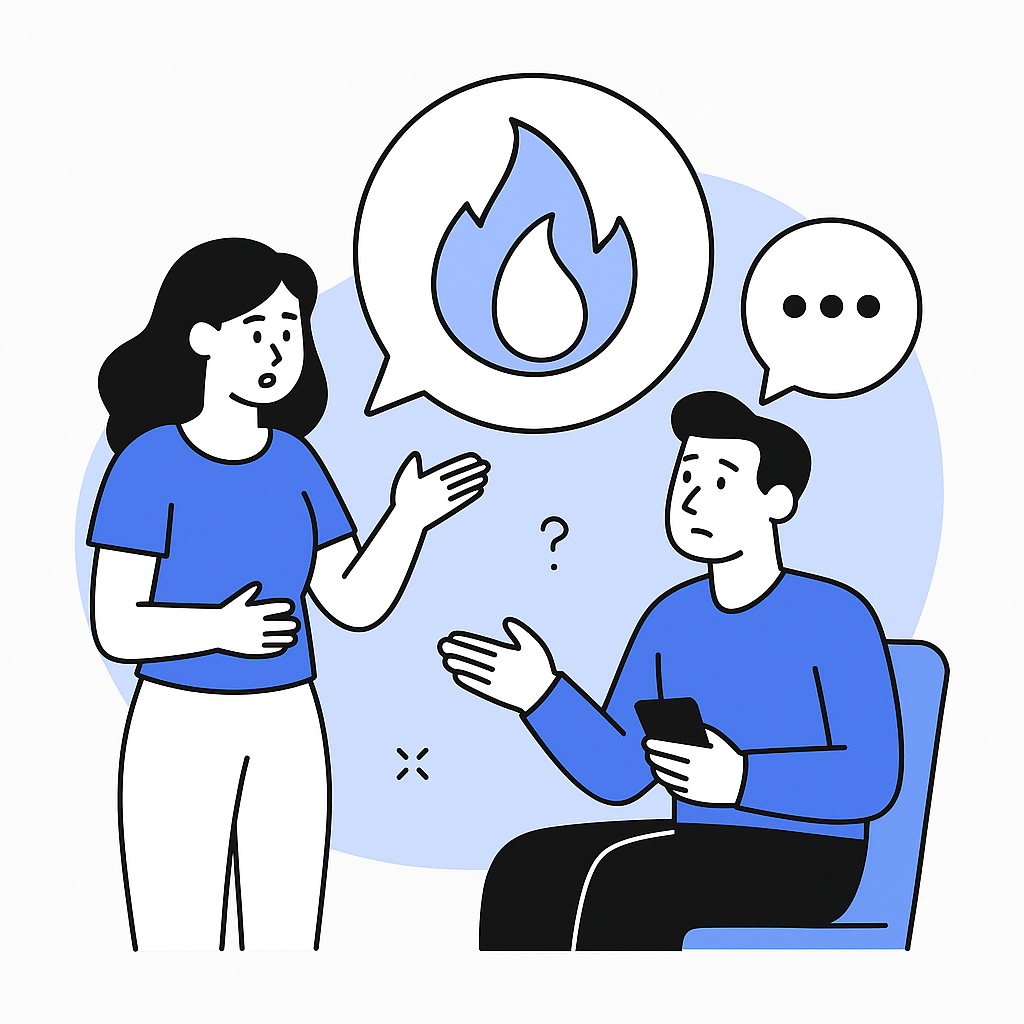
How to fix it:
Establish clear communication protocols. Evalu-8 EHS offers instant alerts and notifications following incident reports, helping managers quickly share critical safety information. Clear communication ensures everyone knows how to prevent incidents from happening again.
Explore Evalu-8's incident & accident feature
Why Evalu-8 EHS is your ideal reporting solution
Evalu-8 EHS isn’t just another software tool, it’s specifically built to solve these common reporting mistakes. Its intuitive design helps you effortlessly manage incident reports, from the moment they occur through detailed analysis and effective communication.
With Evalu-8 EHS, you gain access to easy-to-use mobile reporting, customisable templates for comprehensive reports, powerful analytics to pinpoint trends, and automated alerts to ensure rapid communication. The software takes the guesswork out of reporting, allowing your team to focus more on preventing incidents rather than reacting to them.
Your incident reporting questions answered
Timely reporting ensures accuracy and clarity. The sooner an incident is reported, the clearer the details are, significantly reducing the likelihood of repeat occurrences.
Make reporting quick, easy, and positive. With Evalu-8 EHS’s mobile reporting tools, your employees can quickly log incidents, and you can build a positive culture around safety reporting.
Absolutely! Near misses and minor incidents often signal bigger risks. Properly recording and analysing these allows your team to identify potential hazards before they escalate.
Yes. Using Evalu-8 EHS analytics helps identify patterns and recurring issues, enabling targeted preventive measures, greatly reducing the chance of future incidents.
Evalu-8 EHS is designed to be simple and intuitive, with minimal training required. Support and straightforward guides are provided to make adopting the software easy, even for non-technical users.